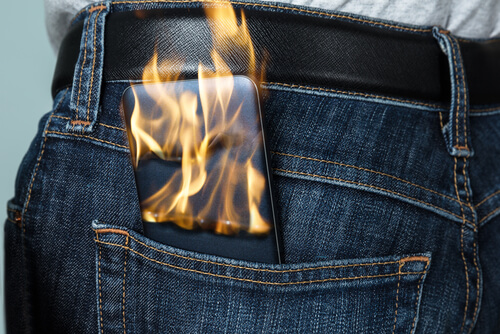
Keramikkondensatoren zeigen eine hohe Empfindlichkeit gegenüber mechanischer Belastung. Selbst geringfügige Biege- und insbesondere Torsionskräfte können schnell zu Rissen und anschließend zu Bränden führen. Brennende Keramikkondensatoren werden in der Elektronikindustrie oft unterschätzt, obwohl sie ein großes Problem darstellen.
Erfahren Sie mehr darüber, wie RoodMicrotec mit Ursachen und potenziellen Gefahren umgeht und Lösungen für dieses Problem findet. Entdecken Sie auch unsere Verfahren zur eindeutigen Erkennung solcher Rissbildungen.
Ursachen von brennenden Keramikkondensatoren
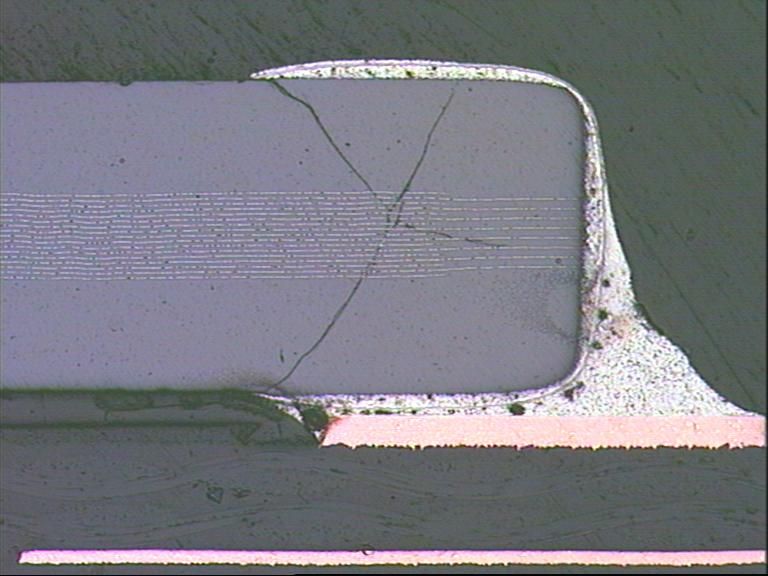
Keramikkondensatoren können aus verschiedenen Gründen Feuer fangen. Mechanische Belastungen wie Biege- und Torsionskräfte können Risse im Keramikmaterial verursachen, was zu Kurzschlüssen und Überhitzung führen kann. Elektrische Überspannungen, unzureichende Entwärmung und schlechte Lötverbindungen sind weitere häufige Ursachen für brennende Keramikkondensatoren.
Speziell die auf Baugruppen gelöteten Keramikkondensatoren sind besonders anfällig. Risse können beispielsweise bei der Bestückung, der Nutzentrennung oder bei der Fixierung der Baugruppe in der Applikation entstehen. Vor allem dann, wenn die Position der Kondensatoren auf der Baugruppe nicht optimal ist.
Die Rissbildung bei Keramikkondensatoren beginnt typischerweise am Rand der Lötstelle auf der Unterseite des Kondensators und verläuft schräg in die Anschlusskappe. In der Anwendung besteht die Gefahr, dass sich das Elektrodenmaterial entlang dieser Risse ausbreitet. Sobald eine Verbindung zwischen benachbarten Elektroden hergestellt ist, wird der Keramikkondensator zu einem Widerstand. Wenn dieser Widerstand niederohmig ist und die Energiequelle über genügend Leistung verfügt, kann dies zu einer Zerstörung und sogar zu einem Brand führen.
Die Hersteller von Bauteilen sind sich dieser Problematik bewusst. Zur Charakterisierung der Empfindlichkeit der Bauteile werden genormte Tests durchgeführt. Dabei werden Kondensatoren auf Leiterplatten gelötet und gebogen. Bei einer Biegebelastung zwischen 3 und 5 mm treten Risse auf, wenn die Fixierungspunkte einen Abstand von 9 cm aufweisen. Noch gefährlicher sind Torsionsbelastungen für die Bauteile. Hier wurden bereits ab einer Torsionsbelastung von 0,5 mm auf 9 cm Risse festgestellt. Leider wird dies jedoch noch nicht standardisiert getestet.
Gefahren von brennenden Keramikkondensatoren
Die Gefahren von brennenden Keramikkondensatoren sind zahlreich und vielfältig. Neben potenziellen Schäden an der Elektronikschaltung können Brände entstehen, die erhebliche Sachschäden und sogar Personenschäden verursachen können. Besonders in sicherheitskritischen Anwendungen wie der Luft- und Raumfahrt oder der Medizintechnik können brennende Keramikkondensatoren verheerende Folgen haben.
Aufgrund der Tatsache, dass nur etwa 1 % dieser Kondensatoren mit Rissen während der elektrischen Endmessung erkannt werden, gelangen viele davon in den Einsatz – und somit in unseren Alltag! Dies birgt ein enormes Risiko, da es in der Anwendung zur Migration von Material kommen kann. Letztendlich kann das dann zu Kurzschlüssen in den Kondensatoren führen, was neben dem Ausfall der elektrischen Baugruppe zusätzlich zu Brandgefahren führt.
Lösungen und Präventionsmaßnahmen
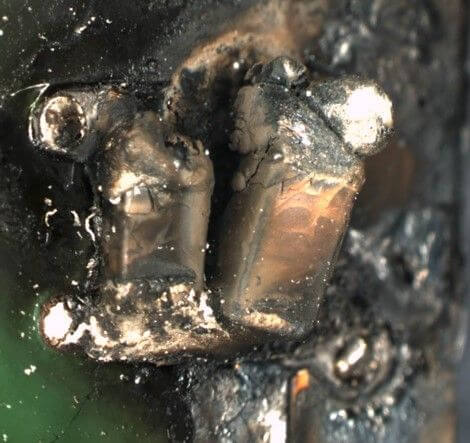
Um das Risiko von brennenden Keramikkondensatoren zu minimieren, sind verschiedene Maßnahmen erforderlich. Dazu gehören die sorgfältige Auswahl und Qualitätsprüfung der Bauteile, die Vermeidung übermäßiger mechanischer Belastung während der Montage und die ordnungsgemäße Entwärmung sowie die Überwachung von Betriebsbedingungen, um elektrische Überspannungen zu verhindern.
Regelmäßige Inspektionen und Tests tragen dazu bei, potenzielle Probleme frühzeitig zu erkennen und evtl. zu beheben. RoodMicrotec bietet hierfür spezielle Prüfverfahren an, um Risse in Keramikkondensatoren frühzeitig zu erkennen und so Ausfälle abzuwenden.
Baugruppendesigner sollten diese Zusammenhänge kennen, denn mit einem geeigneten Layout kann die Gefahr erheblich minimiert werden. Um Gefahren bei der Nutzentrennung zu umgehen wird zum Beispiel empfohlen, Keramikkondensatoren immer mit einem Mindestabstand von 5 mm zur Leiterplattenkante zu platzieren. Bei kleinen Baugruppen ist diese Vorgabe oft nicht realisierbar. Hier lässt sich die Gefahr aber zumindest reduzieren, indem die Kondensatoren so platziert werden, dass die Bauteilachse parallel zum Leiterplattenrand verläuft. Auch die Art der Trennung (zum Beispiel Sägen statt Brechen) kann das Risiko minimieren.
Gleiches gilt für Schrauböffnungen. Da hier die latente Gefahr besteht, dass es beim Verschrauben zu Verwindungen kommt, sollte ein hinreichend großer Abstand gewählt werden oder die Ausrichtung so verlaufen, dass die Bauteilachse entlang von konzentrischen Kreisen um die Öffnung verläuft.
Neben der Anwendung geeigneter Layouts empfiehlt es sich, die Zuverlässigkeit der Kondensatoren beziehungsweise Baugruppen durch physikalische Analysen abzusichern. Konventionelle Analysetechniken waren in der Vergangenheit stets metallografische Schliffe. Allerdings sind diese sehr zeitaufwändig, zerstörend und auf eine Schliffebene beschränkt. Durch die Einzelpräparation ist die Untersuchung zwangsläufig auf wenige Bauteile reduziert. Ein Vorteil ist, dass typische Rissverläufe - beginnend am Rand der Lötstelle und in die Bauteilkappe hinein verlaufend - sehr gut aufgezeigt werden können. Ein Problem bleibt aber die selektive Analyse. Da die Gefahr für die Bauteile von der Montageposition abhängt, garantiert diese Vorgehensweise nicht, dass die am stärksten gefährdeten Bauteile zur Analyse gelangen.
Eindeutiges Analyseverfahren
RoodMicrotec bietet als Alternative ein Testverfahren an, bei dem die Anschlussmetallisierung des Bauteils abgeätzt und anschließend einer lichtoptischen Inspektion unterzogen wird. Dies gewährleistet eine klare Erkennung, da Risse stets an der Oberfläche des Bauteils entstehen und sich am Rand der Anschlussmetallisierung befinden.
Hierbei werden die Kondensatoren schonend von der Baugruppe gelöst. Das anschließende Abätzen der Anschlussmetallisierung erfolgt mittels eines nasschemischen Ätzprozesses, der es ermöglicht, alle Bauteile gleichzeitig in einem Behälter zu behandeln. Die Inspektion erfolgt dann mithilfe eines Stereomikroskops.
Dieses Verfahren ist nicht nur zeitsparend, sondern ermöglicht auch die zeitgleiche Vorbereitung vieler oder sogar aller Teile. Ein weiterer Vorteil: die Bauteile werden nicht beschädigt und es können zusätzliche (3D)-Informationen gewonnen werden, was im Anschluss die Anfertigung metallografischer Schliffe zulässt.
Darüber hinaus liegt ein entscheidender Vorteil dieses Verfahrens in der Möglichkeit, anhand der Position der Risse auf den mechanischen Stress zu schließen. Risse, die durch Biegebelastungen entstehen, verlaufen häufig entlang der gesamten Länge eines Anschlusses. Bei Torsionsstress sind normalerweise beide Anschlüsse betroffen, wobei die Risse jeweils an der gegenüberliegenden Ecke auftreten.
Fazit
Brennende Keramikkondensatoren stellen eine ernsthafte Gefahr dar, die nicht unterschätzt werden sollte. Durch die Identifizierung der Ursachen, die Bewertung der potenziellen Gefahren und die Umsetzung geeigneter Lösungen können Unternehmen und Ingenieure das Risiko von Bränden und Ausfällen durch Keramikkondensatoren minimieren. Ein umfassendes Verständnis dieses Problems ist entscheidend, um die Sicherheit und Zuverlässigkeit elektronischer Systeme zu gewährleisten.
Content Information
Herausgeber: RoodMicrotec GmbH
Quelle: Der Text basiert auf wertvollen Informationen der RoodMicrotec GmbH Fehleranalyse in Stuttgart.
Copyright: Alle in diesem Artikel veröffentlichten Bilder, Videos und Audiodateien unterliegen dem Urheberrecht. Eine Vervielfältigung im Ganzen oder in Teilen ist ohne schriftliche Genehmigung der RoodMicrotec GmbH nicht gestattet.
Für weitere Informationen oder Anfragen zu einer gemeinsamen Kooperation wenden Sie sich bitte an